Amputations in Manufacturing – A New OSHA National Emphasis Program
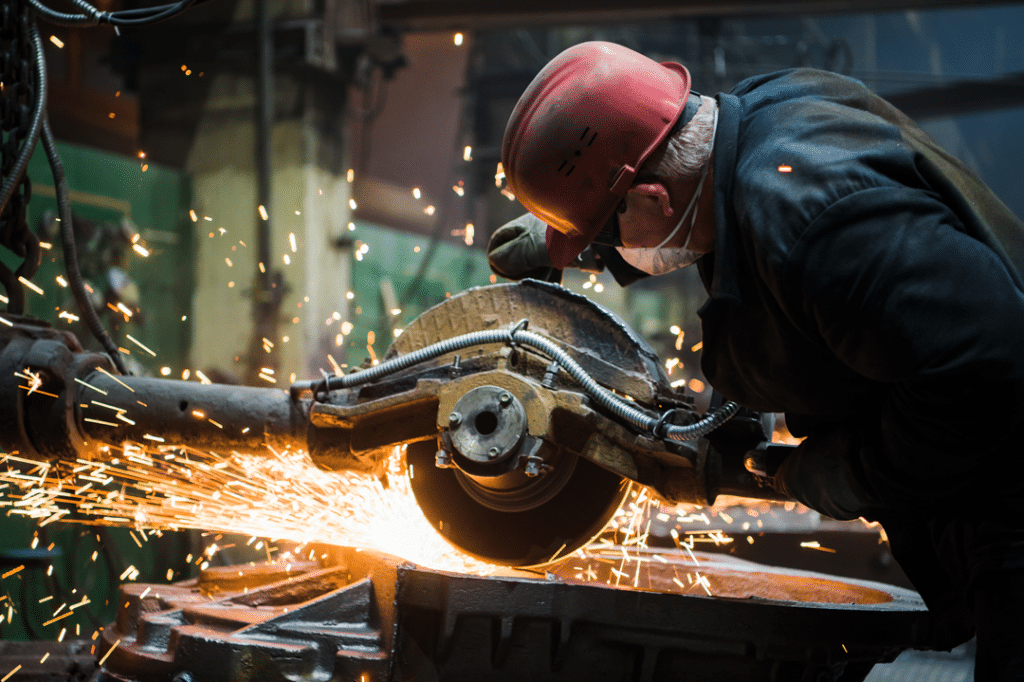
On December 10, 2019 OSHA published CPL 03-00-022, National Emphasis Program on Amputations in Manufacturing Industries. This Instruction supersedes OSHA Instruction CPL 03-00-019, National Emphasis Program on Amputations that was published in August of 2015.
This updated Instruction:
• Revises the coding requirements for amputation inspections in the OSHA Information Systems;
• Revises the targeting methodology to include data from the amputation reporting requirement under 29 CFR § 1904.39;
• Removes Appendix A – Machinery and Equipment from the previous NEP on amputations;
• Removes Appendix B – Related American National Standards Institute
(ANSI)/American Society of Mechanical Engineers (ASME) Standards from the previous NEP;
• Adds a new Appendix A – Amputations Targeting Methodology; and
• Adds a new Appendix B – Covered North American Industry Classification System (NAICS) Codes.
OSHA Area Offices may add, based on local evidence, manufacturing establishments (regardless of the NAICS codes) to the master list where amputation injuries or fatalities related to machinery and equipment have occurred in the five years preceding the effective date of this Instruction. The local evidence may be based on OIS incident data, employer-reported amputations, and workers’ compensation data. Once added, the master list must be re-randomized prior to use after establishments are added.
If you are targeted for an inspection, the CSHO will look for machinery or equipment associated with amputations paying particular attention to employee exposure to nip points, pinch points, shear points, cutting actions, and other points of operation. The CSHO should consider and evaluate employee exposures during setup, regular operation of the machine, clearing jams or upset conditions, making adjustments while the machine is operating, cleaning of the machine, oiling or greasing of the machine or machine pans, scheduled/unscheduled maintenance, and locking out and/or tagging out.
OSHA maintains that machine setup is not normal production; hence LOTO is required. The OSHRC has ruled in OSHA’s favor that setup does not qualify for the Minor Servicing Exemption to 29 CFR 1910.147. Yet, we know that control circuit energy is required in the vast majority of machine setup situations.
FDRsafety has unique expertise to guide employers in tackling setup questions using risk assessment, documenting infeasibility of LOTO and developing an effective Alternative Method to LOTO. The methods we use also guide design and implementation of machine guarding to prevent amputations when equipment is in production.
Mike Taubitz spent many years in top positions at General Motors, including stints as Global Safety Director and Global Regulatory Liaison. He has a strong interest in lean manufacturing and its relationship to safety and in sustainability, and is recognized internationally for his expertise in machine guarding. He assists clients in creating efficient and effective safety programs, especially in manufacturing environments.
For more advice on safety, please call us at (615) 628-8746